Thermoforming: A Manufacturing Process
Here at Fullbore Innovations, we specialize in thermoforming. Our mission is to provide the ATV industry with the most innovative aftermarket body plastic available on the market. Our goal is to design products that exceed industry standards through stellar re-design and the use of proprietary materials in the manufacturing process. Chances are that even if you’ve never heard of thermoforming, you encounter thermoformed plastic every day of your life. Consider your phone case or backpack with plastic parts: they were likely made with thermoformed plastic. Here, we’ve put together an introduction to the thermoforming process so you can understand a little bit more about what we do here at Fullbore Innovations.
History of Thermoforming
Thermoforming has been around for a long time. In the second half of the nineteenth century, Alexander Parks patented a process for using liquid collodion. Collodion is a byproduct of developing photos. Collodion was the first thermoplastic. Some of the earliest examples of molded thermoplastics include smaller items like cosmetic cases, combs, buttons, and toys. However, by the 1930s, innovators developed an automatic thin-sheet roll-fed thermoformer. During this era, plastics became thicker and more widely utilized. For example, in World War II, thermoformed plastics were used for gun turrets and aircraft windshields.
Two Types of Thermoforming
There are two main types of thermoforming. Here at Fullbore Innovations, we specialize in vacuum forming.
Vacuum Thermoforming
Vacuum thermoforming uses heat and pressure to mold plastic sheets into its final configuration. Once a plastic sheet is heated and placed over a male or female mold, a vacuum manipulates the plastic into the desired shape.
Pressure Thermoforming
Pressure thermoforming is very similar to vacuum thermoforming but has additional pressure. In some cases, pressure thermoforming can allow for greater detail and different textures in the plastic.
Stages of Thermoforming
Just like any other manufacturing process, there are several stages of thermoforming. A typical thermoforming process goes as follows:
Design Prototype
Most thermoformed plastic products start as a CAD model or an engineered drawing. Here at Fullbore Innovations, our engineers and designers are involved in developing or improving client models and designs. No matter what you have in mind for your ATV, we can help you form it with proprietary materials. We also have plenty of commercial clients who need specially formed plastics for their businesses. Fullbore Innovations has a wide range of usable products available for custom vacuum forming.
Mold and Material Selection
After you have decided on a specific design for your product, our engineers will help you decide which type of plastic and mold is appropriate for you and your project. We will help you make these decisions based on the type and size of the product as well as the production run.
Production
After our engineers and designers have helped you design the product you have in mind, it’s time for us to produce it for you! All of the logistics of production are handled in-house, so you don’t have to worry about sourcing materials or labor. To get started on your next ATV plastics project, call Fullbore Innovations today!
Roll Stand
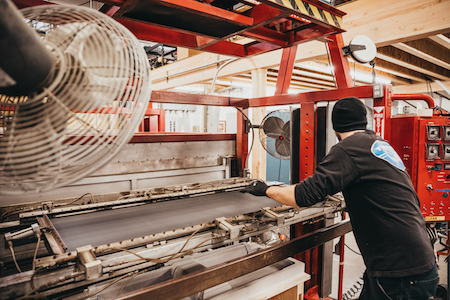
Get started today with custom ATV plastics from Fullbore Innovations in Portland, Oregon!
Material In-Feed
The plastic sheets are fed through the machine.
Heat
The materials are heated to a pliable temperature until it sready for molding.
Forming Station
As we mentioned, we specialize in vacuum thermoforming here at Fullbore Innovacations. At the forming stations, the plastic molding compresses against the film and a vacuum helps form it into specific shapes with added pressure.
Trimming
After the product has been formed, we trim off any excess plastic and then move on to any other production processes such as painting or assembly as agreed to during the design process.
The Benefits of Thermoforming
There are numerous benefits to thermoforming when it comes to production and manufacturing processes.
Affordable
Thermoforming is an affordable, low cost manufacturing process. Plastic sheets are one of the most affordable raw materials available for forming ATV products. The vacuum thermoforming process scales well, which makes large production runs economical for your business.
Flexibility
Vacuum thermoforming is a flexible manufacturing process. Not only can we make a wide range of ATV plastics at Fullbore Innovations, but we are able to make numerous types of plastic products of varying complexity and detail.
Speed
Thermoforming can result in fast lead times for large volume manufacturing. Excess material during the manufacturing process can be collected, reground, and formed back into plastic sheets for additional manufacturing as well.
How Can Fullbore Innovations Help You?
Fullbore Innovations is an NW based company located in Portland, Oregon, about 3 hours away from our secondary headquarters in Coos Bay. We have a backyard that is over 5000 acres just for testing grounds for our new products. Our first company was a thermoforming and composite operation producing parts for aircraft and other mfg. Industries over 20 years ago. As enthusiasts of off-road motorsports, we recognized the need for a high-end alternative to OEM plastic. Being a well-established, full-service facility, we decide to aim some horsepower towards our passion. Never looking back, we began development on a plastic specifically designed for our sport. Our demands on the supplier were to develop a chemical resistant material with extreme durability, high gloss surface in a full spectrum of colors. Our enthusiasm was contagious. The result was a high impact, polymer alloy, stronger than most plastics. After obtaining the proprietary right to the new material, we began to form a team of key people to help launch our new division. With the help of state-of-the-art equipment, computer software, and robotics, our team has taken our products to the very top. We are pleased to offer you the most innovative products on the market today.